DIY Kontiki / Torpedo .
Instructions for assembling the "ekonotiki" bilge pump powered torpedo .
This is meant mainly for New Zealand and the few other countries where longline fishing from the beach is legal . The 'kontiki' I designed pulls out at least 15 hooks on 50kg line to a distance of about 500m in 25 minutes .
These are the instructions for the simplest design I could conceive for just about anybody to make their own torpedo .It will do the job but some changes will make for a more efficient model for those prepared to go that extra bit . The T-junction is simple but effective but obviously the upright bit causes a bit of resistance as does the coke bottle . My next model will require a bit more skill and will consist of a straight 100mm tube with the back end heated up for batteries to be pushed in - so they can also be removed , a lid at the rear for less resistance , and a long thin flotation tube possibly 50 to 100cm above the main pipe , which will make the torpedo more functional in white water [froth] as it will be lower and also do away with the resistance of the upright of a T-junction .It will also be made using the 13000 litre / hour bilge pump which is twice as strong as the prototype .There will be a saving of $45 on the piping , an extra $60 for the pump and the cost of an extra battery to ensure efficiency due to the extra current draw of an 18 amp pump . Meanwhile , however , here are the instructions for the prototype .... The early design featured in the June edition of "bay fisher " and was mentioned again in the July edition .
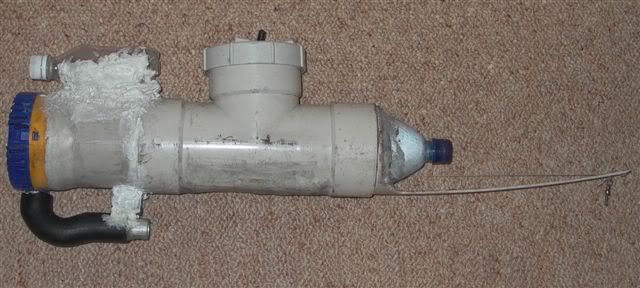
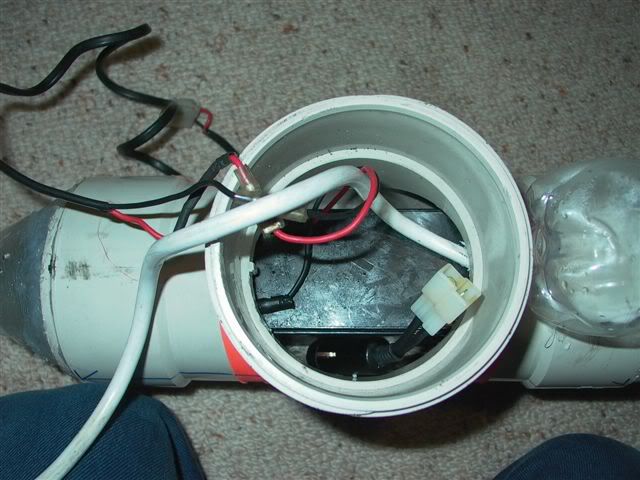
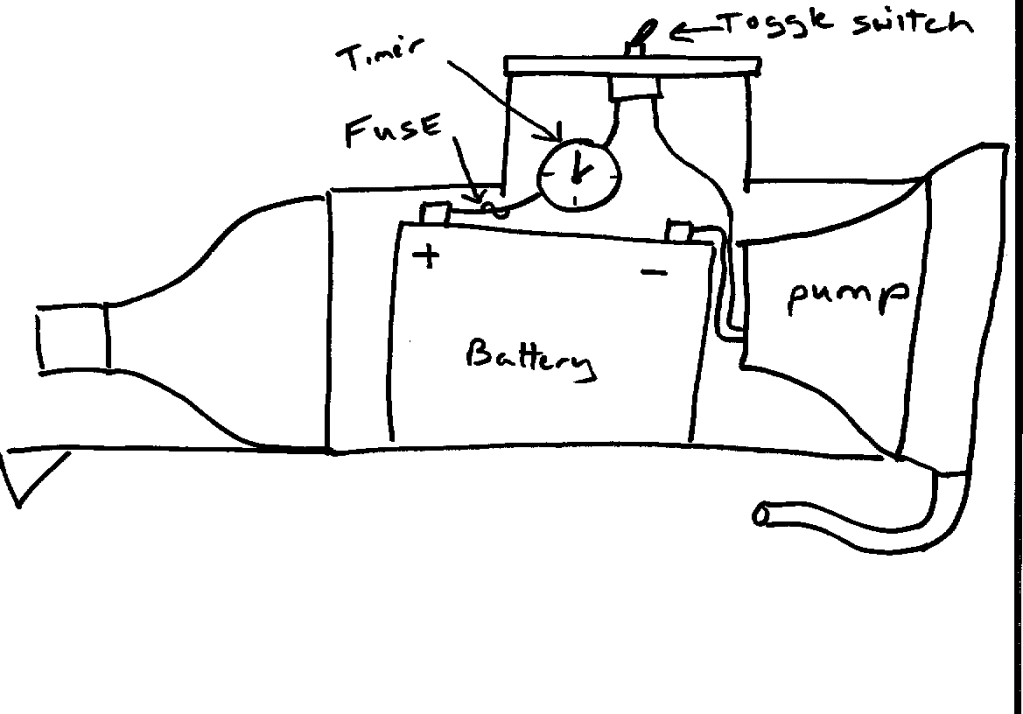
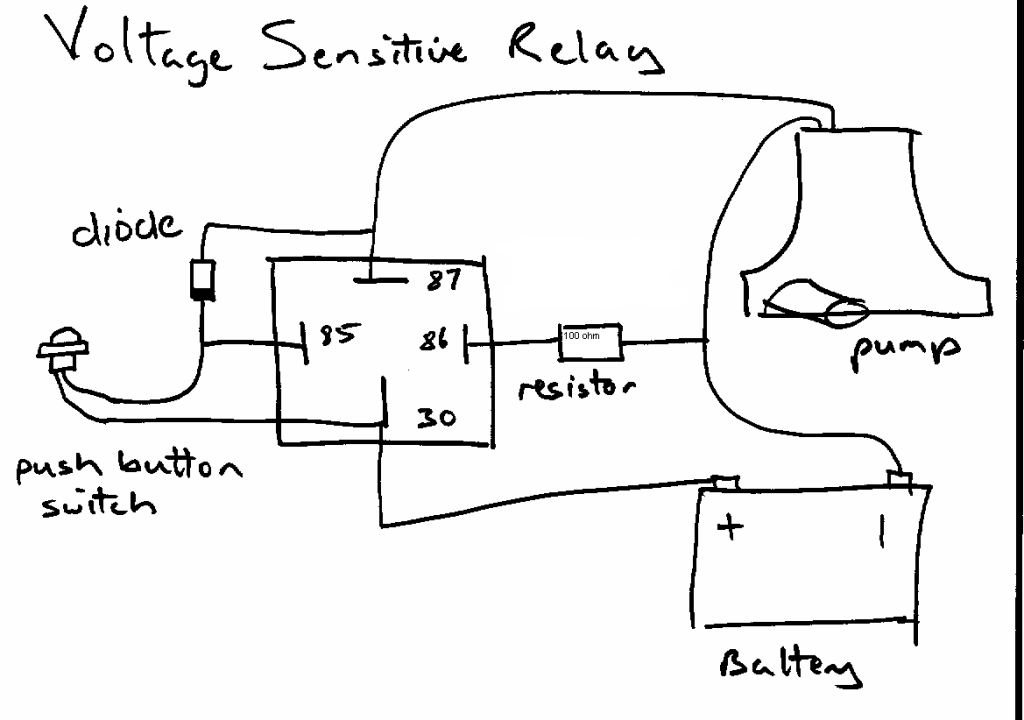
.
You will need:
1.] Bilge pump. , at least 1500gallons/hr / 6500 litres/hr . About $85 for the Hella 10 amp model .I suggest using the same pump as I used since no others have been properly tested yet and a higher capacity pump uses a lot of battery power which causes other complications but I include the following information anyway : Burnsco marine has a 3000g/hr / 13000l/hr pump that draws 18 amps and will make a torpedo that is twice as strong.The whole advantage of a bilge pump is that they are designed to sit in seawater .Some bilge pumps may need their bases cut away to allow direct flow as many are designed to suck from the sides .
Warning ! Bilge pumps do not like to be run "dry" .When mounting the pump , roughen up the surface for better glue contact . If you are paranoid like me you can drill some small holes around the perimeter of the front pipe [not in the bilge pump !] for the glue to sink into and get a better grip .Remember that some pumps have different bases so you may need to drill holes in the bottom of the pump to let water in the front of the torpedos movement .
19/06/04 Today I went into Burnsco marine and they have a special on bilge pumps . The one I used was a hella 1500g/h or 6500l/h .
They have a TMC 2000 for $95[2000g/h] ,TMC 2500 $179 , and a TMC 3000 for $139 which is twice the output of mine . .
The interesting thing about the TMC 2500 is that it has its outlet at exactly the right angle which will require no bends , but it is rated at the same current draw as the 3000 which suggests an efficiency fault or someone has made a spelling error . The 2500 was the most expensive and was 500g/h less than the 3000 so I bought a 3000 and will have to get a decent pipe/radiator hose of 32mm for it .... time to give the jet turbo power ! { I gave up on the 3000 model and stuck with the more reliable prototype design eventually}
2.] T-junction 100mm pipe . The T-junction with twist on lid makes it easier to work with the wiring and timer , it is reasonably watertight but in any case sits above the water line most of the time .The T-junction is sold with a piece of pipe on one end so it is not necessary to buy an extra meter like I did which ended up being cut into a tail . With a line pulling at the back , a tail is not totally necessary but will make it go straighter . even a piece of plastic pipe will do the job for the tail and being flexible will make for better traveling through waves since it will flex instead of tilting too much.Make the front pipe 100mm long , if the pump is heavier than a 10 amp model you could make it about 50mm longer for extra flotation .
3.] Water bottle . A spring water bottle from K-Mart has an o/d of 104mm which is the exact i/d of "100mm" tubing . If you cut it in half , and glue it up the tail end ,it seals off quite nicely and provides a lid for
drainage if you get water in the torpedo , and some nice aero-dynamics .
4.] Glue . I used kitchen and bathroom white silicone because it dries quicker and has a more rigid hold while the clear stuff is a bit stretchy . Now that I have finished cutting and experimenting I will get something
more permanent like Araldite which should also look neater and strip it down and put it together properly , though this silicone is quite easy to work with and has held quite well . Just remember to roughen up the
surface of the bilge pump before you glue it because it is quite smooth and pulls out of the glue with little effort .I stripped my torpedo down once I "perfected" the design and bought some "knead it " 'aqua ' from K-mart on special for $6 a roll . You have 20 - 30 minutes to work with it before it goes hard and it did a beautiful job holding the bilge pump in ... it still remains to be seen how long it lasts but it supposedly can be used to repair boats underwater !
5.] Battery . A 7,2 a/h battery fits nicely into the inside of the T-junction when you cut out a rectangle from the bottom and glue it in .{ make a layer of glue under the battery to insulate it from the sea water , cold can affect a battery's output by up to 50% } A battery should ideally be 3 times the a/ hour rating that you require . For a 10 amp motor a 7,2 amp hour battery would keep it going for 0,72 of an hour or 43 minutes . A third of that would be 14 minutes use to guarantee a maximum lifespan from the battery . Many people just run the battery dead flat which means the acid goes into the plates and they break down faster . A good compromise would be to use it for 20 minutes maximum even though it would go for 40 minutes on one charge .
I have connected up a cigarette lighter adapter to my battery so it can be charged from my vehicle .A 1/4 charged battery is 12 volts , fully charged is 12,7 volts .If you don't want to cut and glue a battery in , a
heat gun makes the plastic piping very flexible and the battery squeezes in perfectly . You would have to do this at the tail end and then make a flap/lid that seals off nicely so batteries can be removed or
swapped around with charged batteries, the piping shrinks a bit when it cools so put some spacers in when you first slide the battery in and pull them out once it cools .This is an alternative to buying a $45 T-junction in that you could buy 1 meter of piping for $15 , push the battery/s up the rear , and make a lid/flap at the back for changing batteries and setting the timer .
Optional. ... "soft seal" spray for preventing corrosion from sea water which will one day find its way inside . Spray over everything , battery terminals , wiring and switches - don't get it on bare switch contacts . This is a precautionary measure that will save you the frustration of having to pull everything apart if corrosion sets in .
Jet size . This is very important . My first experiment was to see how high I could make the jet shoot by squeezing the nozzle , assuming that this would give maximum thrust . My assumption was wrong because the volume was restricted resulting in a slow movement . If you just have the water pouring out of the hose , which has an inner diameter of 25mm which is the outer diameter of the bilge pump outlet , the water slows down because it has gone into a larger area , you must get the area back to the 22.5mm [approx] that it was coming out of at the pump to regain the original speed . I believe that a slightly higher speed could be achieved by certain laws of physics by making the outlet ever so slightly smaller than the 22.5mm jet . I fitted a 32mm electrical wiring gland which makes the outlet adjustable for easy experimenting . I could not get a noticeable improvement on 22.5mm so have decided to leave it at that in the knowledge that less pressure on the pump means a longer life .I was told by a water pump technician that a "positive displacement " pump would achieve better results with a smaller nozzle but the centrifugal bilge pump does not react the same way with restrictions .
The piece of pipe in front is 100mm long and without the coke bottle it would point downwards . A bit of fancy fibreglass-work could make it more streamlined . A 375 ml bottle would also do the job as the torpedo floats perfectly with the coke bottle about halfway under the water .This also ensures that the front of the pump is always under water and doesn't suck air
Night fishing ? Instead of a coke bottle , mount a glass jar on the front and put in a bicycle flashing LED available for $2 from a dollar-value store .
Shorter and heavier means more stability going through waves and better momentum , which also reduces the effect of waves .Two batteries means a heavier torpedo and slightly more time to build up speed but once it has that speed it will be harder to slow down by oncoming waves/swells .
Tail . A tail is not entirely necessary when towing something but can be useful for tying things to . A flexible tail would also make for easier movement through swells .Thinner is better as it causes less resistance .
Another good idea for the tail is to have a " fan - shaped " tail with a row of holes in it so that , depending on the current , you can connect the line off centre to steer the torpedo left or right .
Wiring . Run an earth wire straight from the battery to the pump .Preferably put a 15 amp fuse from the battery positive , to the timer then to the switch . Since bilge pumps don't like to run dry it is best to also have a toggle switch with a rubber boot over it on the lid so you can set the timer , close the lid , and then put it in the water and flick the switch on .The fuse is not to protect the pump , it is so that if there is a short in the pump or wiring the switches and wiring don't get damaged .
Voltage sensitive relay . I have designed a crude " voltage sensitive relay " which does away with the need for an expensive timer and gets the most out of the batteries .This has worked but needs a fully charged battery if you are going to use a push-button to energize it , another option is to remove the outer casing of the relay and just squeeze the contacts together when you need it to start .... it will stay in until the battery drops to 11 volts . On the attached diagram you will see how to wire it up . The ' 30 ' terminal is the positive input . When a button is pushed [ or a simple toggle switch is flicked on and off again ] , the relay pulls in and supplies " 87 " with power , which also supplies " 85 " with power , through a diode , which keeps the relay on . The " 86 " terminal provides an earth through a resistor [ 100 ohms , R1650 , Dick Smith no. ] which has the effect of halving the voltage at the relay coil since the coil resistance is also 68 ohms .
Now a 12 volt relay can work at 6 volts , but as the power runs out of the battery and its voltage drops to 11 volts , the relay now has 4 volts at its coil , and 7 volts across the resistor , and lets go around this voltage . This means that the battery voltage never drops below 10 which could happen if a timer is set too long .. With the mkII which has 2 batteries I have wired up the batteries separately so I can have 2 settings ... one or both batteries .It would make sense to put the relay in a small plastic bag for water protection .
I also welcome suggestions on improvements .
Thanks , Desmond . { Springbok kontikis }
Eventually I also drew up some plans for a bilge pump modified to take a propeller and one person who bought the plans to help him finish his project sent me a picture of his 'rig' along with a picture of a few large snapper he caught the next weekend . His version was quite a bit bigger than mine .
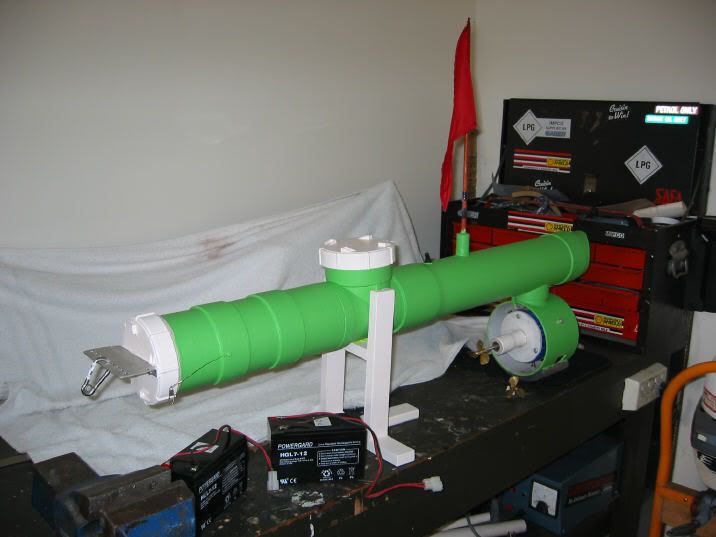
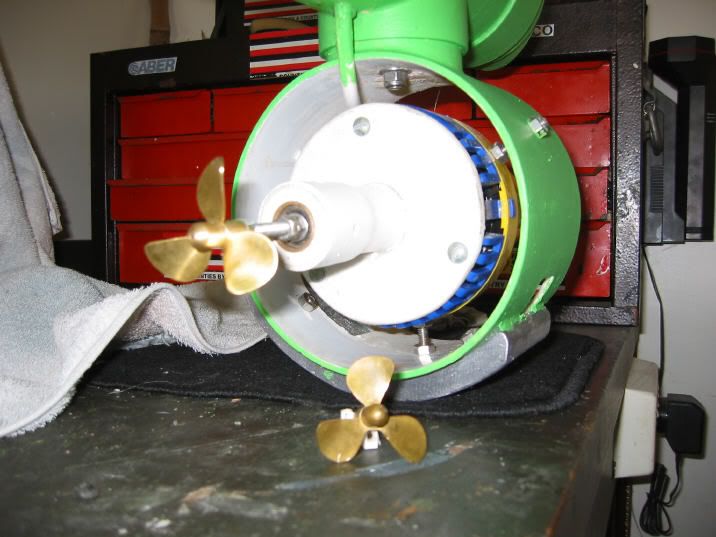
Here are the plans for making the propeller version along with the next project I designed - a wiper motor driven winch for reeling the line back in .....
Instructions for assembling the "ekonotiki" bilge pump powered torpedo .
This is meant mainly for New Zealand and the few other countries where longline fishing from the beach is legal . The 'kontiki' I designed pulls out at least 15 hooks on 50kg line to a distance of about 500m in 25 minutes .
These are the instructions for the simplest design I could conceive for just about anybody to make their own torpedo .It will do the job but some changes will make for a more efficient model for those prepared to go that extra bit . The T-junction is simple but effective but obviously the upright bit causes a bit of resistance as does the coke bottle . My next model will require a bit more skill and will consist of a straight 100mm tube with the back end heated up for batteries to be pushed in - so they can also be removed , a lid at the rear for less resistance , and a long thin flotation tube possibly 50 to 100cm above the main pipe , which will make the torpedo more functional in white water [froth] as it will be lower and also do away with the resistance of the upright of a T-junction .It will also be made using the 13000 litre / hour bilge pump which is twice as strong as the prototype .There will be a saving of $45 on the piping , an extra $60 for the pump and the cost of an extra battery to ensure efficiency due to the extra current draw of an 18 amp pump . Meanwhile , however , here are the instructions for the prototype .... The early design featured in the June edition of "bay fisher " and was mentioned again in the July edition .
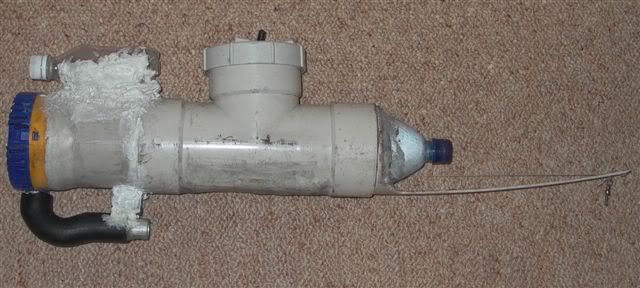
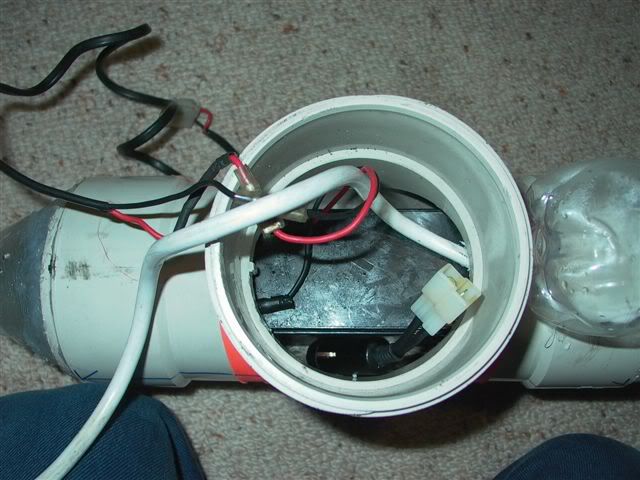
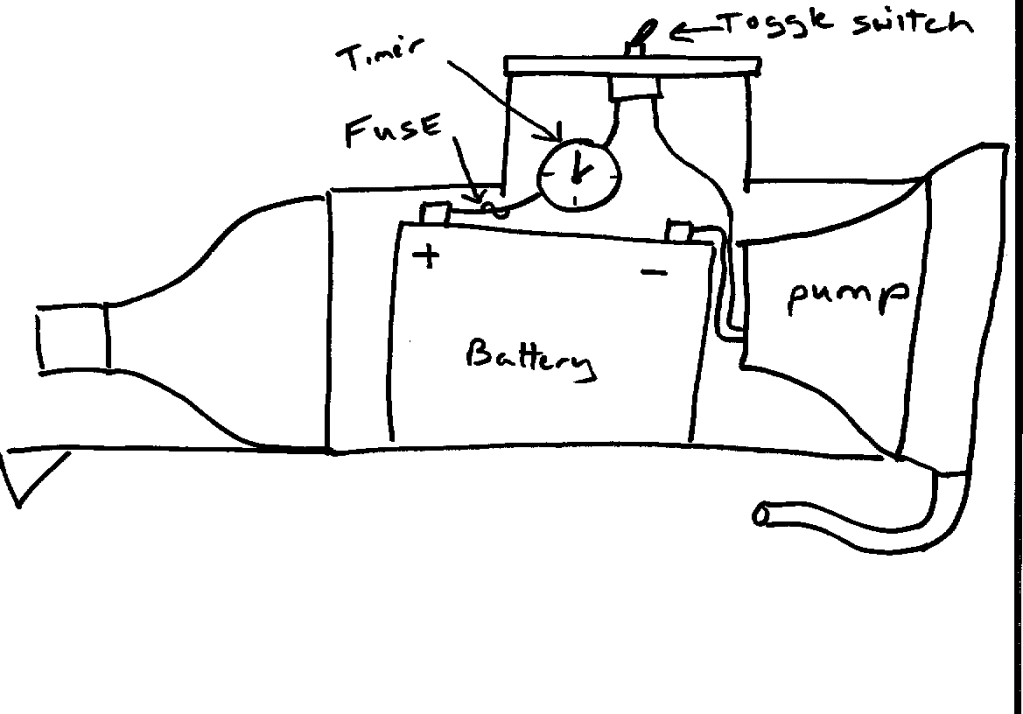
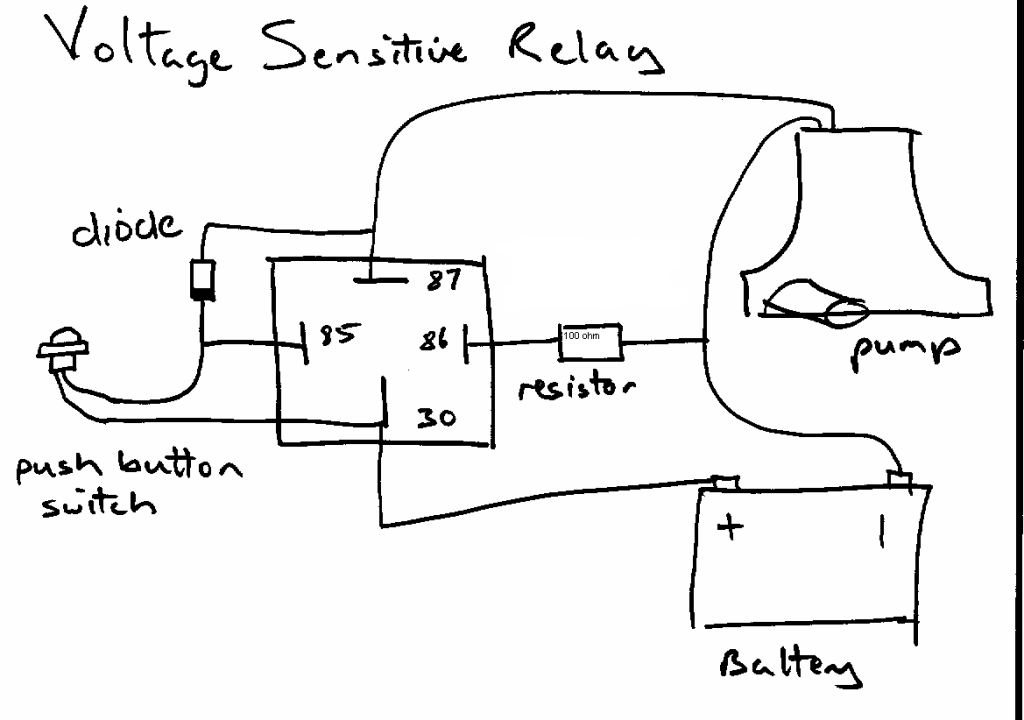
.
You will need:
1.] Bilge pump. , at least 1500gallons/hr / 6500 litres/hr . About $85 for the Hella 10 amp model .I suggest using the same pump as I used since no others have been properly tested yet and a higher capacity pump uses a lot of battery power which causes other complications but I include the following information anyway : Burnsco marine has a 3000g/hr / 13000l/hr pump that draws 18 amps and will make a torpedo that is twice as strong.The whole advantage of a bilge pump is that they are designed to sit in seawater .Some bilge pumps may need their bases cut away to allow direct flow as many are designed to suck from the sides .
Warning ! Bilge pumps do not like to be run "dry" .When mounting the pump , roughen up the surface for better glue contact . If you are paranoid like me you can drill some small holes around the perimeter of the front pipe [not in the bilge pump !] for the glue to sink into and get a better grip .Remember that some pumps have different bases so you may need to drill holes in the bottom of the pump to let water in the front of the torpedos movement .
19/06/04 Today I went into Burnsco marine and they have a special on bilge pumps . The one I used was a hella 1500g/h or 6500l/h .
They have a TMC 2000 for $95[2000g/h] ,TMC 2500 $179 , and a TMC 3000 for $139 which is twice the output of mine . .
The interesting thing about the TMC 2500 is that it has its outlet at exactly the right angle which will require no bends , but it is rated at the same current draw as the 3000 which suggests an efficiency fault or someone has made a spelling error . The 2500 was the most expensive and was 500g/h less than the 3000 so I bought a 3000 and will have to get a decent pipe/radiator hose of 32mm for it .... time to give the jet turbo power ! { I gave up on the 3000 model and stuck with the more reliable prototype design eventually}
2.] T-junction 100mm pipe . The T-junction with twist on lid makes it easier to work with the wiring and timer , it is reasonably watertight but in any case sits above the water line most of the time .The T-junction is sold with a piece of pipe on one end so it is not necessary to buy an extra meter like I did which ended up being cut into a tail . With a line pulling at the back , a tail is not totally necessary but will make it go straighter . even a piece of plastic pipe will do the job for the tail and being flexible will make for better traveling through waves since it will flex instead of tilting too much.Make the front pipe 100mm long , if the pump is heavier than a 10 amp model you could make it about 50mm longer for extra flotation .
3.] Water bottle . A spring water bottle from K-Mart has an o/d of 104mm which is the exact i/d of "100mm" tubing . If you cut it in half , and glue it up the tail end ,it seals off quite nicely and provides a lid for
drainage if you get water in the torpedo , and some nice aero-dynamics .
4.] Glue . I used kitchen and bathroom white silicone because it dries quicker and has a more rigid hold while the clear stuff is a bit stretchy . Now that I have finished cutting and experimenting I will get something
more permanent like Araldite which should also look neater and strip it down and put it together properly , though this silicone is quite easy to work with and has held quite well . Just remember to roughen up the
surface of the bilge pump before you glue it because it is quite smooth and pulls out of the glue with little effort .I stripped my torpedo down once I "perfected" the design and bought some "knead it " 'aqua ' from K-mart on special for $6 a roll . You have 20 - 30 minutes to work with it before it goes hard and it did a beautiful job holding the bilge pump in ... it still remains to be seen how long it lasts but it supposedly can be used to repair boats underwater !
5.] Battery . A 7,2 a/h battery fits nicely into the inside of the T-junction when you cut out a rectangle from the bottom and glue it in .{ make a layer of glue under the battery to insulate it from the sea water , cold can affect a battery's output by up to 50% } A battery should ideally be 3 times the a/ hour rating that you require . For a 10 amp motor a 7,2 amp hour battery would keep it going for 0,72 of an hour or 43 minutes . A third of that would be 14 minutes use to guarantee a maximum lifespan from the battery . Many people just run the battery dead flat which means the acid goes into the plates and they break down faster . A good compromise would be to use it for 20 minutes maximum even though it would go for 40 minutes on one charge .
I have connected up a cigarette lighter adapter to my battery so it can be charged from my vehicle .A 1/4 charged battery is 12 volts , fully charged is 12,7 volts .If you don't want to cut and glue a battery in , a
heat gun makes the plastic piping very flexible and the battery squeezes in perfectly . You would have to do this at the tail end and then make a flap/lid that seals off nicely so batteries can be removed or
swapped around with charged batteries, the piping shrinks a bit when it cools so put some spacers in when you first slide the battery in and pull them out once it cools .This is an alternative to buying a $45 T-junction in that you could buy 1 meter of piping for $15 , push the battery/s up the rear , and make a lid/flap at the back for changing batteries and setting the timer .
6.] Hose . The hose that joins onto the bilge pump outlet and bends at 90 degrees to the outlet jet should not be ribbed as that wastes a lot of energy . A radiator hose with the correct bend is ideal and easy to
work with and can be bought new for about $15 or sometimes the wreckers have a barrel full of them for next to nothing . The jet outlet should be the same size as the inner diameter of the bilge pump outlet for
maximum thrust .Even though narrowing the outlet down produces jets of water that shoot further it still produces less thrust due to less volume . I have cut a small piece of hose to glue between the outlet and
the main body of the torpedo to keep it stable .Find a piece of piping the same size as the bilge pump outlet with the same inner diameter and glue it in the end to ' tweak ' the thrust .On my prototype I used a CH1047 radiator hose from Repco [$12.50] which was the perfect size , but the wreckers gave me a hose out of their bin for the MKII.
7.] Switch/timer . I have mounted a toggle switch , with a screw on rubber boot to waterproof it , on the lid of the T-junction for experimenting . The same switch will eventually be in line with a mechanical timer from
an old stove so that the timer can be set while the switch is in the "off " position . Then once it is ready to send out a flick of the switch on the top will start it up .An alternative I have been considering for a timer is to tie the line to the front of the pump , loop it to the tail end tied on by a single strand of cotton ... a jerk breaks the cotton and turns the torpedo around .. a procedure I learned while doing test runs .[ I am not the jerk by the way ] . This can be taken a step further by connecting the same line that moves from the rear to the front , to the switch on top , by a piece of elastic which will then turn the switch off in the same motion . I am also thinking of the possibility of a flap that pivots on the bottom for minimum resistance when it is going forward , but when you pull the torpedo backwards and the water pressure forces the flap down , it trips the switch off , and disconnects the line from the back so the torpedo can be turned around and pulled back later [This might not be practical due to the amount of stretch in 500metres of line . I eventually pulled the timer out of my tabletop oven that cost $60 [only $10 more than buying a timer] and I will fit a toggle switch in place of the timer for my oven to work .
8.] Flag . A kite can be bought at the "dollar value " shop for $2 and butchered to make a flag .
9.] Coke Bottle . Placing the coke bottle above the front section keeps the front from pointing down . I have noticed though that a bigger motor seems to cause the torpedo to pull to the right a bit . This would be due to the torsion of the motor making the torpedo twist to the side a bit , placing the jet to the left of centre , causing it to veer to the right [ depending on what direction your motor turns ] . The solution for this is to place 2 floatation devices [coke bottles if you don't have something more dignified] above the pump - the further apart they are the more stable it will be . Since a 600mm coke bottle does the job , two 300mm bottles placed above the pump , one to either side , will stabilise the torpedo and prevent it pulling to the side . This is all dependent on the weight of the torpedo and how far from the centre the jet is , the further from the centre the more pronounced the effect of twisting will be , but don't make it so close to the body that it wastes energy on turbulence against the body . We will end up with the "starship enterprise " design soon . A moderately distanced jet with 2 flotation devices acting as "outriggers ".
work with and can be bought new for about $15 or sometimes the wreckers have a barrel full of them for next to nothing . The jet outlet should be the same size as the inner diameter of the bilge pump outlet for
maximum thrust .Even though narrowing the outlet down produces jets of water that shoot further it still produces less thrust due to less volume . I have cut a small piece of hose to glue between the outlet and
the main body of the torpedo to keep it stable .Find a piece of piping the same size as the bilge pump outlet with the same inner diameter and glue it in the end to ' tweak ' the thrust .On my prototype I used a CH1047 radiator hose from Repco [$12.50] which was the perfect size , but the wreckers gave me a hose out of their bin for the MKII.
7.] Switch/timer . I have mounted a toggle switch , with a screw on rubber boot to waterproof it , on the lid of the T-junction for experimenting . The same switch will eventually be in line with a mechanical timer from
an old stove so that the timer can be set while the switch is in the "off " position . Then once it is ready to send out a flick of the switch on the top will start it up .An alternative I have been considering for a timer is to tie the line to the front of the pump , loop it to the tail end tied on by a single strand of cotton ... a jerk breaks the cotton and turns the torpedo around .. a procedure I learned while doing test runs .[ I am not the jerk by the way ] . This can be taken a step further by connecting the same line that moves from the rear to the front , to the switch on top , by a piece of elastic which will then turn the switch off in the same motion . I am also thinking of the possibility of a flap that pivots on the bottom for minimum resistance when it is going forward , but when you pull the torpedo backwards and the water pressure forces the flap down , it trips the switch off , and disconnects the line from the back so the torpedo can be turned around and pulled back later [This might not be practical due to the amount of stretch in 500metres of line . I eventually pulled the timer out of my tabletop oven that cost $60 [only $10 more than buying a timer] and I will fit a toggle switch in place of the timer for my oven to work .
8.] Flag . A kite can be bought at the "dollar value " shop for $2 and butchered to make a flag .
9.] Coke Bottle . Placing the coke bottle above the front section keeps the front from pointing down . I have noticed though that a bigger motor seems to cause the torpedo to pull to the right a bit . This would be due to the torsion of the motor making the torpedo twist to the side a bit , placing the jet to the left of centre , causing it to veer to the right [ depending on what direction your motor turns ] . The solution for this is to place 2 floatation devices [coke bottles if you don't have something more dignified] above the pump - the further apart they are the more stable it will be . Since a 600mm coke bottle does the job , two 300mm bottles placed above the pump , one to either side , will stabilise the torpedo and prevent it pulling to the side . This is all dependent on the weight of the torpedo and how far from the centre the jet is , the further from the centre the more pronounced the effect of twisting will be , but don't make it so close to the body that it wastes energy on turbulence against the body . We will end up with the "starship enterprise " design soon . A moderately distanced jet with 2 flotation devices acting as "outriggers ".
Jet size . This is very important . My first experiment was to see how high I could make the jet shoot by squeezing the nozzle , assuming that this would give maximum thrust . My assumption was wrong because the volume was restricted resulting in a slow movement . If you just have the water pouring out of the hose , which has an inner diameter of 25mm which is the outer diameter of the bilge pump outlet , the water slows down because it has gone into a larger area , you must get the area back to the 22.5mm [approx] that it was coming out of at the pump to regain the original speed . I believe that a slightly higher speed could be achieved by certain laws of physics by making the outlet ever so slightly smaller than the 22.5mm jet . I fitted a 32mm electrical wiring gland which makes the outlet adjustable for easy experimenting . I could not get a noticeable improvement on 22.5mm so have decided to leave it at that in the knowledge that less pressure on the pump means a longer life .I was told by a water pump technician that a "positive displacement " pump would achieve better results with a smaller nozzle but the centrifugal bilge pump does not react the same way with restrictions .
The piece of pipe in front is 100mm long and without the coke bottle it would point downwards . A bit of fancy fibreglass-work could make it more streamlined . A 375 ml bottle would also do the job as the torpedo floats perfectly with the coke bottle about halfway under the water .This also ensures that the front of the pump is always under water and doesn't suck air
Night fishing ? Instead of a coke bottle , mount a glass jar on the front and put in a bicycle flashing LED available for $2 from a dollar-value store .
Shorter and heavier means more stability going through waves and better momentum , which also reduces the effect of waves .Two batteries means a heavier torpedo and slightly more time to build up speed but once it has that speed it will be harder to slow down by oncoming waves/swells .
Tail . A tail is not entirely necessary when towing something but can be useful for tying things to . A flexible tail would also make for easier movement through swells .Thinner is better as it causes less resistance .
Another good idea for the tail is to have a " fan - shaped " tail with a row of holes in it so that , depending on the current , you can connect the line off centre to steer the torpedo left or right .
Wiring . Run an earth wire straight from the battery to the pump .Preferably put a 15 amp fuse from the battery positive , to the timer then to the switch . Since bilge pumps don't like to run dry it is best to also have a toggle switch with a rubber boot over it on the lid so you can set the timer , close the lid , and then put it in the water and flick the switch on .The fuse is not to protect the pump , it is so that if there is a short in the pump or wiring the switches and wiring don't get damaged .
Voltage sensitive relay . I have designed a crude " voltage sensitive relay " which does away with the need for an expensive timer and gets the most out of the batteries .This has worked but needs a fully charged battery if you are going to use a push-button to energize it , another option is to remove the outer casing of the relay and just squeeze the contacts together when you need it to start .... it will stay in until the battery drops to 11 volts . On the attached diagram you will see how to wire it up . The ' 30 ' terminal is the positive input . When a button is pushed [ or a simple toggle switch is flicked on and off again ] , the relay pulls in and supplies " 87 " with power , which also supplies " 85 " with power , through a diode , which keeps the relay on . The " 86 " terminal provides an earth through a resistor [ 100 ohms , R1650 , Dick Smith no. ] which has the effect of halving the voltage at the relay coil since the coil resistance is also 68 ohms .
Now a 12 volt relay can work at 6 volts , but as the power runs out of the battery and its voltage drops to 11 volts , the relay now has 4 volts at its coil , and 7 volts across the resistor , and lets go around this voltage . This means that the battery voltage never drops below 10 which could happen if a timer is set too long .. With the mkII which has 2 batteries I have wired up the batteries separately so I can have 2 settings ... one or both batteries .It would make sense to put the relay in a small plastic bag for water protection .
I also welcome suggestions on improvements .
Thanks , Desmond . { Springbok kontikis }
Eventually I also drew up some plans for a bilge pump modified to take a propeller and one person who bought the plans to help him finish his project sent me a picture of his 'rig' along with a picture of a few large snapper he caught the next weekend . His version was quite a bit bigger than mine .
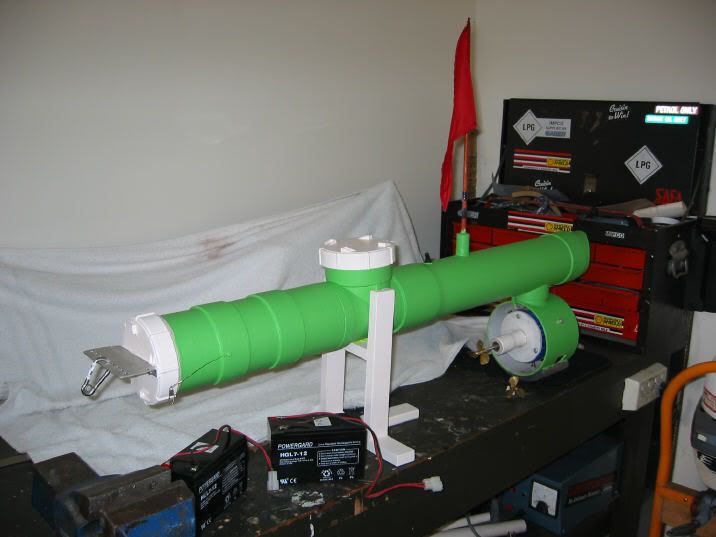
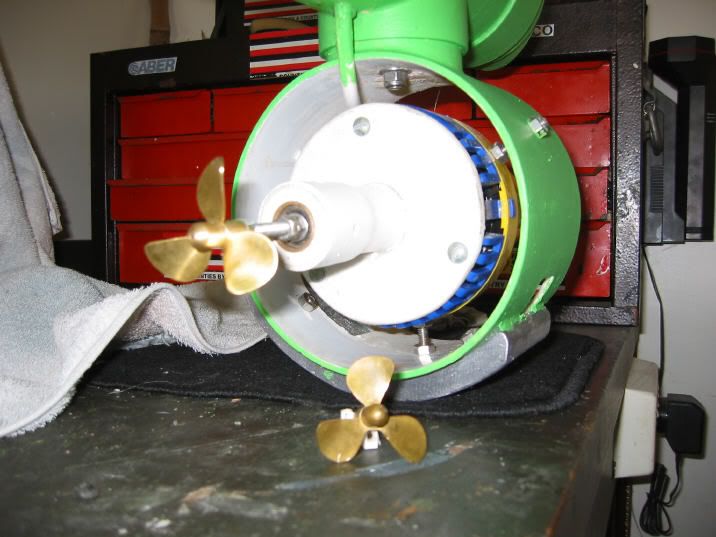
Here are the plans for making the propeller version along with the next project I designed - a wiper motor driven winch for reeling the line back in .....
Before you start :
1.) These plans are a guide only , it worked for me but you may have other/better ways to do it .
2.) A bilge pump is not a "thrust "motor , it does not necessarily have a washer at the top of the motor to prevent wear from pressure pushing upwards on it . The thrust must be directed to the front of the plastic pipe .
3.) Though the hella bilge pump is rated at 10 amps I have it running at 15 at the moment . I don't expect it to give trouble but still need to do a few more runs before I am convinced . Generally anything electrical is like a welder , it can run continuously at a low current draw but has a duty cycle for higher currents , as it draws more current it gets hotter and so needs a certain cooling off period before being used again . With the motor sitting in seawater it should cool off a bit quicker though we must remember it is insulated by plastic and a bit of air so don't count on it . It will also have a maximum current draw wher the wiring to the brushes will blow like a fuse after a few turns . One of the props I made had a massive thrust but drew 30 amps from the motor . Once I have perfected the brassprop design I will give it a run with that prop and either sacrifice a good motor or find that we have a winner and that the motor can handle that type of punishment .
4.) There are two options : 1.] making a motor that pushes and 2 .] making a motor that pulls . 1.] I have chosen this way because it is easier to make in that the force pushing against the plastic pipe actually strengthens the supporting framework instead of trying to pull it apart . With a pushing motor water that is sucked in to the prop can come from any direction and the thrust has no obstruction .The prop pushes on its drive shaft and so the small pipe cannot fall off while running .The disadvantage is that you must be sure to direct the force to the plastic pipe to prevent motor wear .
2.] A motor that pulls has the advantage that the pump most likely has a washer at its base for wear and it will pull against this washer . A pulling prop can be pulled off the drive shaft if not 100% secured . A pulling prop will direct its thrust straight at the motor behind it and create turbulence . need I say more ....
First you will need a Hella 10 amp 1500gph bilge pump . If you use a different pump you will have to play around with other modifications .
You will also need : A sheet of polypropylene at least 120 mm diameter .
A piece of "32mm " plastic pipe .
A length of tubing about 10mm diam , about 7 mm inner diam or have one made up .
2 or 3 17 mm nuts , preferably stainless .
A washer .[ or two ]
A small propeller , about the same size as the white plastic impeller inside the pump , or make one out of the polypropylene .
Remove the blue plastic base . { When you push the clips in observe the small lip on the clips , if that is not pushed down enough to release the clips can break }
Remove the rubber ring that holds the plastic impeller in place and remove the impeller .
Cut a circular piece of polypropylene with a hole in the middle for the plastic pipe to fit snugly inside . Drill holes to fit this circle to the blue base with self tappers .
Check your distances by pushing the pipe hard against the base and glue it in place with marine silicone .[ only glue it to the disc you have made .
Drill a few holes in the pipe to let water in , the pump seal will be damaged if it runs dry .You may want to wrap a bit of cloth around the holes to keep sand out .
The hardest part is the small pipe . If you have the means to so so you could drill a hole in the stainless shaft of the motor and put a split pin through to hold it on .
I chose to drill a small hole in the small pipe and tap a thread and tighten a small bolt up against the shaft , which has a flat spot , to stop it slipping .
You must also cut a round "bush" to go inside the plastic pipe for the small pipe to go through and which will take the thrust of the prop .
Where the pipe comes out of the bush you must cut a thread or find another means of securing the prop [ maybe a grub screw ] .
I have used 3 stainless nuts and a washer so that I can tighten the washer against the plastic pipe , to put the main force on there instead of on the inside of the motor , and to lock the prop in place .
The propeller I bought from "Bay hobby supplies "Tauranga (07) 577 6240 . It never had a part number but cost $22,50 .
It is fairly easy to make a prop out of polypropylene if you cut the shape out and heat it up with a heat gun and give it a twist . I made one the size of the base of the pump and then machined it down smaller and smaller on the lathe to get the current draw right .
The bilge pump motor spins relatively fast so a smaller prop is needed . I am fairly confident the gearing down that speed to about 1/3 and making a prop with good thrust will get much better results . Until then we must use the small prop / high speed rotation .
Contact me at dvdowns@xtra.co.nz if you have any questions or suggestions .{ springbok kontikis }
This winch will not pull in the whole weight of the line for you but it is a compromise that will turn the spool while you pull in the weight of the line to make the job twice as fast for a one man setup .
I paid $30 for the motor and $15 for the pulleys from the wreckers .A battery will be about $30 so for less than $100 you can have something that does half the job of a $1200 winch .
The winch-assist was designed as a cheap alternative to the $1200 models that do all the work .
You can use any wiper motor and pulley/s but the ones I used are readily available from the wreckers .
You will need :
1.) Wiper motor [ Mitubishi L200 A478 ] this one has a nice braket on it that makes it easier to mount onto your exisiting spool .
2.) Pulley [ Mitsubishi L300 A 905 ] twin size pulley for 2 speeds .
3.) 7 amp hour 12 volt battery , this size is big enough to do the job but a bigger battery will last longer .
4.) Fan belt , any old belt will do , as long as it fits in the pulley .
5.) One half of a 2 piece alternator pulley . Go in to your local auto electrician , they will most likely have a box full of old pulleys .
Undo the bracket that the motor mounts onto and rotate it so that it sticks out 90 degrees to the motor to make for easier mounting .
Take the wiper motor and cut the drive part with the socket on it so that it can be drilled to fit the pulley , that is the way I did it but welding will do a better job .
{ I used 2 bolts but 3 smaller bolts will prevent the pulley pulling off centre under load }
On the spool , you will have to take off the plastic cap on the end of the through-bar and pull the frame outwards to get the half-pulley on . Centralise it and drill 3 holes and tighten with self tappers .
Fit the fan belt and use its length to align where the motor will mount . The belt must not be too tight , you want it to slip when it starts to get tight to prevent the spool being wound too tight and to stop the spool from falling over when under too much tension .If you can't get a haly-pulley you can make something since there is already a round bit on the spool , it just needs something to keep the belt on it .
Wiring : The wiper motor has 2 sppeds and the pulley has two sizes giving a total of 4 possible speeds .
The white wire must be earthed .[ direct to the battery ]
The blue and orange wire is for slow speed and the blue and black wire is for fast speed .
You can either just put on push-on terminals on those wires which you will have to plug on to get the motor going or you can take the wires to a switch .
With a 3 way toggle switch you can take a wire from battery positive to the centre pin and put the blue/orange and blue/black on the outer pins so flicking the switch in either direction will give 2 different speeds .
Either mount the motor with spacers directly below the pulley or loosen the main bolt holding the spool , give it a slight twist to face the bottom pulley , and give the motor bracket a slight twist so they face each other properly and the belt doesn't climb off .
1.) These plans are a guide only , it worked for me but you may have other/better ways to do it .
2.) A bilge pump is not a "thrust "motor , it does not necessarily have a washer at the top of the motor to prevent wear from pressure pushing upwards on it . The thrust must be directed to the front of the plastic pipe .
3.) Though the hella bilge pump is rated at 10 amps I have it running at 15 at the moment . I don't expect it to give trouble but still need to do a few more runs before I am convinced . Generally anything electrical is like a welder , it can run continuously at a low current draw but has a duty cycle for higher currents , as it draws more current it gets hotter and so needs a certain cooling off period before being used again . With the motor sitting in seawater it should cool off a bit quicker though we must remember it is insulated by plastic and a bit of air so don't count on it . It will also have a maximum current draw wher the wiring to the brushes will blow like a fuse after a few turns . One of the props I made had a massive thrust but drew 30 amps from the motor . Once I have perfected the brassprop design I will give it a run with that prop and either sacrifice a good motor or find that we have a winner and that the motor can handle that type of punishment .
4.) There are two options : 1.] making a motor that pushes and 2 .] making a motor that pulls . 1.] I have chosen this way because it is easier to make in that the force pushing against the plastic pipe actually strengthens the supporting framework instead of trying to pull it apart . With a pushing motor water that is sucked in to the prop can come from any direction and the thrust has no obstruction .The prop pushes on its drive shaft and so the small pipe cannot fall off while running .The disadvantage is that you must be sure to direct the force to the plastic pipe to prevent motor wear .
2.] A motor that pulls has the advantage that the pump most likely has a washer at its base for wear and it will pull against this washer . A pulling prop can be pulled off the drive shaft if not 100% secured . A pulling prop will direct its thrust straight at the motor behind it and create turbulence . need I say more ....
First you will need a Hella 10 amp 1500gph bilge pump . If you use a different pump you will have to play around with other modifications .
You will also need : A sheet of polypropylene at least 120 mm diameter .
A piece of "32mm " plastic pipe .
A length of tubing about 10mm diam , about 7 mm inner diam or have one made up .
2 or 3 17 mm nuts , preferably stainless .
A washer .[ or two ]
A small propeller , about the same size as the white plastic impeller inside the pump , or make one out of the polypropylene .
Remove the blue plastic base . { When you push the clips in observe the small lip on the clips , if that is not pushed down enough to release the clips can break }
Remove the rubber ring that holds the plastic impeller in place and remove the impeller .
Cut a circular piece of polypropylene with a hole in the middle for the plastic pipe to fit snugly inside . Drill holes to fit this circle to the blue base with self tappers .
Check your distances by pushing the pipe hard against the base and glue it in place with marine silicone .[ only glue it to the disc you have made .
Drill a few holes in the pipe to let water in , the pump seal will be damaged if it runs dry .You may want to wrap a bit of cloth around the holes to keep sand out .
The hardest part is the small pipe . If you have the means to so so you could drill a hole in the stainless shaft of the motor and put a split pin through to hold it on .
I chose to drill a small hole in the small pipe and tap a thread and tighten a small bolt up against the shaft , which has a flat spot , to stop it slipping .
You must also cut a round "bush" to go inside the plastic pipe for the small pipe to go through and which will take the thrust of the prop .
Where the pipe comes out of the bush you must cut a thread or find another means of securing the prop [ maybe a grub screw ] .
I have used 3 stainless nuts and a washer so that I can tighten the washer against the plastic pipe , to put the main force on there instead of on the inside of the motor , and to lock the prop in place .
The propeller I bought from "Bay hobby supplies "Tauranga (07) 577 6240 . It never had a part number but cost $22,50 .
It is fairly easy to make a prop out of polypropylene if you cut the shape out and heat it up with a heat gun and give it a twist . I made one the size of the base of the pump and then machined it down smaller and smaller on the lathe to get the current draw right .
The bilge pump motor spins relatively fast so a smaller prop is needed . I am fairly confident the gearing down that speed to about 1/3 and making a prop with good thrust will get much better results . Until then we must use the small prop / high speed rotation .
Contact me at dvdowns@xtra.co.nz if you have any questions or suggestions .{ springbok kontikis }
This winch will not pull in the whole weight of the line for you but it is a compromise that will turn the spool while you pull in the weight of the line to make the job twice as fast for a one man setup .
I paid $30 for the motor and $15 for the pulleys from the wreckers .A battery will be about $30 so for less than $100 you can have something that does half the job of a $1200 winch .
The winch-assist was designed as a cheap alternative to the $1200 models that do all the work .
You can use any wiper motor and pulley/s but the ones I used are readily available from the wreckers .
You will need :
1.) Wiper motor [ Mitubishi L200 A478 ] this one has a nice braket on it that makes it easier to mount onto your exisiting spool .
2.) Pulley [ Mitsubishi L300 A 905 ] twin size pulley for 2 speeds .
3.) 7 amp hour 12 volt battery , this size is big enough to do the job but a bigger battery will last longer .
4.) Fan belt , any old belt will do , as long as it fits in the pulley .
5.) One half of a 2 piece alternator pulley . Go in to your local auto electrician , they will most likely have a box full of old pulleys .
Undo the bracket that the motor mounts onto and rotate it so that it sticks out 90 degrees to the motor to make for easier mounting .
Take the wiper motor and cut the drive part with the socket on it so that it can be drilled to fit the pulley , that is the way I did it but welding will do a better job .
{ I used 2 bolts but 3 smaller bolts will prevent the pulley pulling off centre under load }
On the spool , you will have to take off the plastic cap on the end of the through-bar and pull the frame outwards to get the half-pulley on . Centralise it and drill 3 holes and tighten with self tappers .
Fit the fan belt and use its length to align where the motor will mount . The belt must not be too tight , you want it to slip when it starts to get tight to prevent the spool being wound too tight and to stop the spool from falling over when under too much tension .If you can't get a haly-pulley you can make something since there is already a round bit on the spool , it just needs something to keep the belt on it .
Wiring : The wiper motor has 2 sppeds and the pulley has two sizes giving a total of 4 possible speeds .
The white wire must be earthed .[ direct to the battery ]
The blue and orange wire is for slow speed and the blue and black wire is for fast speed .
You can either just put on push-on terminals on those wires which you will have to plug on to get the motor going or you can take the wires to a switch .
With a 3 way toggle switch you can take a wire from battery positive to the centre pin and put the blue/orange and blue/black on the outer pins so flicking the switch in either direction will give 2 different speeds .
Either mount the motor with spacers directly below the pulley or loosen the main bolt holding the spool , give it a slight twist to face the bottom pulley , and give the motor bracket a slight twist so they face each other properly and the belt doesn't climb off .